01989 563941
Specialistsin EMC Solutions
TC Shielding manufactures EMC gaskets made from conductive silicones, fluorosilicones, fabric wrap and other products for use in shielding electronic enclosures and connectors, to achieve electromagnetic compatibility.
ISO 9001 REGISTERED
We are ISO 9001 certified,
VIEW ISO CERTIFICATE
ensuring we meet your needs through an effective quality management system.
FAST LEAD TIMES
We are conductive silicone manufacturers, meaning we are in complete control of when you get your product.
CONTACT US NOW
WORLDWIDE AGENTS
Not in the UK? We have agents located all over the world who are ready to assist you with your EMC shielding enquiry.
CONTACT AN AGENT NEAR YOU
ABOUT US
THE CONDUCTIVE ELASTOMER SPECIALISTS
Established since 1991, we manufacture EMC gaskets for the defence, aerospace and telecommunications industries all over the world, as well as supplying product for various other commercial projects and applications.
At TC Shielding we pride ourselves in offering unparalleled technical support. This comes in the form of in depth advice regarding grooves, hardware and environmental assessments, torque calculations, etc.
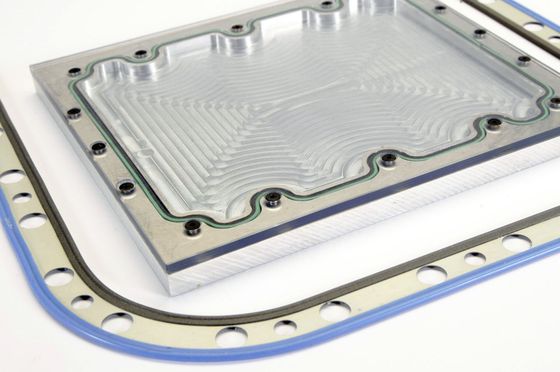
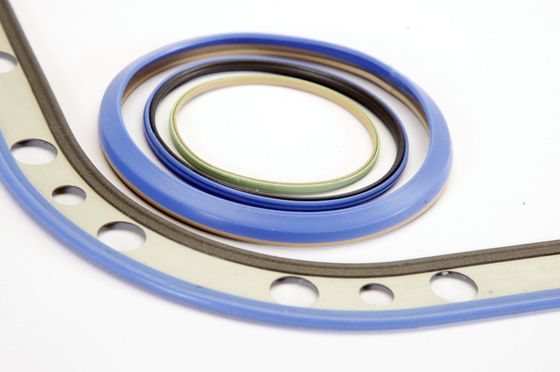
OUR SERVICES
EXTRUDED PROFILES
Describe a company feature.
FLAT GASKETS
Describe a company feature.
MOULDED GASKETS
Describe a company feature.
FABRIC / FOAM GASKETS
Describe a company feature.
CONTACT US
Whether you need technical assistance regarding your application, or know exactly what you want and are just looking for fast quotation, we are waiting for you to get in touch!
LATEST NEWS
ISO 9001
Describe a company feature.
WORLDWIDE AGENTS
Describe a company feature.
DESIGN SERVICE
Describe a company feature.